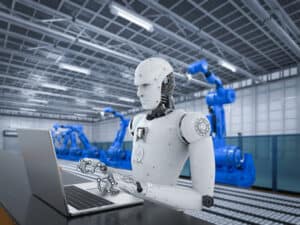
RTInsights talks with Siemens about the need to convert to smart factories, the technologies that can help, and the benefits that automakers can derive from making the change.
Auto manufacturers and their Tier 1 suppliers face challenging times. Economic issues are forcing them to improve operations, regulations are driving the need to adopt more sustainable practices throughout the end-to-end manufacturing cycle, and customers want autos equipped with the latest technologies. Traditional factories and the manufacturing operations they support do not provide the flexibility or capability to meet the demands of these changes. Increasingly, automakers find they must quickly modernize their facilities to smart factories.
RTInsights recently sat down with Greg Roth, Director of Automotive and Transportation at Digital Industries Software at Siemens, to talk about the need to convert to smart factories, the technologies that can help, and the benefits that automakers can derive from making the change.
Here is a summary of our conversation.
RTInsights: What type of intelligent technologies are needed to convert a regular factory to a smart factory?
Roth: We can break it into two areas. The first thing you need is the virtualization of the factory and the ability to have a digital twin of the factory environment. That lets you develop new ideas, what-ifs, and move equipment around, all virtually. Essentially, we’re taking and representing your assembly line or production line digitally. So, you can do simulations to see how robots work together. You can do ergonomic studies with humans to see if the equipment’s set up in the right way so as to not cause them to have back pain or issues in getting the equipment in the right place. You have the ability then to do all these different what-if scenarios virtually. That allows you to develop a much more efficient production or manufacturing environment without the cost overruns and launch delays associated with building and testing physically to find problems. All the issues are identified virtually, achieving a “get it right the first time” strategy.
The other part of this is you need to actually implement it. You need to actually have equipment running. And it has to be intelligent. It has to be able to run and make decisions and basically produce the quality and throughput you need to achieve costs and meet customer delivery goals.
Those are the two technology sets. We also need what we like to refer to as intelligent production excellence. That is where your line is running with some intelligence. It can make decisions, see problems, and react to these problems, sometimes by self-correcting or self-organizing ways and others by informing people of issues even before they happen.
This is an ongoing activity through production. It doesn’t stop. The goal is to make sure your line is always up and running and achieving the quality and costs that are required for the company.
RTInsights: Many auto manufacturers do not have vast expertise in these technologies. What problems and issues typically occur when they try to implement them?
Roth: Companies that are new to this type of technology approach face problems in two main areas.
One is you have old equipment. Many companies do not have the option to go out and purchase all the high-tech new equipment. They’ve invested in this equipment, and they just want to make sure they use what they have. Some of this older equipment uses communication protocols that are difficult to connect into modern smart ecosystems.
As such, companies must retrofit with the newer technologies. That will then allow them to move to an intelligent production excellence phase.
To give you an idea of how old some of the systems are, I’ve been in companies where some of the equipment is still running DOS, the old disc operating system technologies. If you want to connect via high-tech IoT wireless, that equipment has to be retrofitted. Can it be done? Yes. But you do have to invest. And that’s part of the understanding. If you’re taking older equipment, you do have to invest to be able to allow it to work within these new modern infrastructures and ecosystems.
They must implement IoT technologies and IT and OT integrations. Making such changes, companies find that there is a lot of data being gathered, which is a critical element to the whole smart manufacturing concept. The problem, then, is that sometimes it’s just too much data. You’re trying to monitor things, and you are not able to make sense of it all.
Years ago, when I was in the industry, people were doing SPC. They were monitoring their lines and all the physical process controls, but they didn’t do anything with it. So, they weren’t taking advantage of the data because they were overwhelmed with data.
When making the change to smart factories, manufacturers need edge computing, artificial intelligence, machine learning, and coding and scripting to do data analytics. They can then enable some self-organizing, self-correcting activities to help minimize disruptions.
A good example is if you’re monitoring, let’s say, a motor for a piece of production equipment, and you can sense the voltages or temperatures are spiking, which indicates it needs maintenance. A normal way to handle this is to schedule a maintenance person to investigate. If there is a problem with the motor, the line might go down for quite a bit of time as they get a new motor. And that’s a huge disruption.
What you really want to do with that information is process it and forecast when the motor will go down. Then, you can order the replacement parts ahead of time automatically and schedule the maintenance automatically. All of these things working together minimize the disruption.
So, you’re not only recording and getting this data, but you have to figure out what to do with it. With the new AI and machine learning technologies, that’s making things a lot better.
RTInsights: Where/how should a manufacturer begin? A single work cell, assembly line, or an entire facility?
Roth: Of course, we’d love to say, “Yeah, do the entire factory,” but you still have to start somewhere. And if a company is just getting into smart manufacturing, you start wherever you can, and usually, it’s at the single work cell level.
You put in some type of vision system or monitoring right there to catch a quality issue. Or if, let’s say, you’re doing drilling operations, you can check for chatter and temperature to indicate when the drill bit may wear out. Those are little things you can start to do, and those have an impact.
Now, the real beauty of smart manufacturing is more at the ecosystem level, where everything’s working together with one another. So, it doesn’t help you if you have a work cell, for example, that you’re able to improve your overall equipment effectiveness, but downstream, there’s another piece of equipment that’s always going down. You’re not going to get the improvement you want.
Typically, you start with a work cell, but really, you want to move to the production line or assembly level. That’s when you’re going to see the benefits of smart manufacturing. Ultimately, you want to go the whole factory or facility level because then there are interactions within the ecosystem at many levels. Now, everything’s working together with your AGVs and your warehouse inventory processes. That will affect the manufacturing line that you focused on, but now the benefits are starting to spread to the plant level.
So, start with a single work cell. Then, quickly go to the assembly line or production line to really see any benefit. Then take it to that whole production plant level because otherwise, you’re not really going to get all the benefits and efficiencies. And when you start talking about sustainability topics, this is where you really start seeing the benefit at more of the facility level in energy usage efficiencies and reducing waste.
RTInsights: How does Siemens help auto manufacturers and their Tier 1 suppliers evolve their factories and operations?
Roth: We do it in multiple ways. First, we have the software technology, as we were just discussing, the PLM and the digital industries software part of Siemens AG. We focus on the data backbones and the product lifecycle management aspects down into manufacturing. So, we provide the software at this operating system level for the manufacturing environment.
You also get the benefits of doing virtual development and simulation development of your product line. You can do what-if scenarios and virtual commissioning. But then the beauty is, at the company level, we are an industrial company. It’s not just that we make software to help people do it. As a company, Siemens actually makes products. We actually use our own software and our own technologies to make actual products.
So, we have expertise and knowledge that a lot of our competitors do not. We live and breathe this. We can go into a customer site and provide the needed technologies and expertise to implement them successfully.
Additionally, we have factory automation, motion control, and process automation solutions, as well as customer services. These are in addition to our software activities. There are hardware solutions designed exactly for customers to use.
Along with these solutions, we have the expertise and over 170 years of experience doing this. That gives us quite a competitive advantage. Other companies are just familiar with the software side of things; we provide the whole picture. We can go in and make you successful, both at the software level and down to the actual hardware and implementation level.
RTInsights: Can you give examples and discuss the benefits manufacturers realize in making the change?
Roth: In my job here at Siemens, we represent the automotive manufacturing industry. I actually was in the automotive industry for many years and was involved in manufacturing and product development. I can tell you numerous anecdotes and stories, but trying to generalize or summarize it, that’s where I think the focus really should be.
We can start off with one example of using smart manufacturing technologies that are very timely or applicable to the sustainability question. A premier German OEM implemented technology across the board. They were doing the virtual development of their manufacturing line, where they could see ahead of time if the equipment and manufacturing processes worked the way they wanted before investing and implementing the physical line. That lets them go from virtual to the actual hardware implementation, and it works the first time. It is such a critical aspect to the whole product development and manufacturing process.
Without this approach, many companies, when they go to launch, have to go through numerous designs, build, test, and break iterations to achieve success. They design and develop a line or work cell, but they don’t know if it really works. And then, when they actually implement the hardware, they find all sorts of problems. There are interferences, or the flows don’t work right, or the PLC doesn’t correctly work on the equipment, and then they have to fix it. That takes time, and it slows down the launch process.
When you start doing virtual development, companies feel more comfortable that whatever they do virtually will actually work the first time. And then that allows them to do what-if studies to explore new ways of manufacturing and optimize energy and costs.
So, one German company did a lot of work on reducing their energy usage by smartly developing their production line. They developed an understanding of what things could be turned off during different phases of a production work order to save money. For example, that would include the ability to shut down an air compressor and then reduce the cooling fluids to certain equipment because the equipment was in idle mode.
Knowing this still does not solve the problem. They don’t have the technology to shut things down automatically. They would have to leave that air compressor or cooling system running. But, if they integrated IT and OT, that would allow them to get those things automated. And that’s the key underlying aspect of smart manufacturing, the automation of many, many tasks.
The German company was able to achieve significant energy savings because they could figure everything out and organize everything virtually before they implemented the plant. Then, they could execute it with automation.
Some other good examples in the automotive world where they’re using this is in what’s called the live twin aspect of smart manufacturing. A live twin is basically keeping an eye on your production line and then reacting to it based on the inputs you’re getting. For example, if you have spot welds being done, the live digital twin can monitor the equipment currents and voltages for those spot-welding operations and forecast what spot welds need to be further quality checked.
Over time, it learns. Not only can it identify these quality question marks in their spot-welding process, but it can also feed the insights to an audit testing group, which can then check things out. But that helps eliminate the need to have to do these quality checks throughout all the body in white spot welds. So now you can focus on the ones that are really suspect.
Then there’s a larger closed-loop manufacturing aspect to smart manufacturing, whereas these learnings that you get through your manufacturing processes go through an AI or some type of data analytics process to understand them. That lets you address the issues locally with self-correction and self-organizing capabilities. Maybe the voltages have gone down. Why is that? Maybe there’s something in the equipment that needs to be adjusted, and that can be handled right away to make sure your production qualities are good.
There’s also a feedback loop to product development where they can say, look, if you do spot welds in a certain way, we’re seeing there’s more quality issues. Maybe the voltage and current issues tend not to work as well as indicators of quality. That information can be fed back earlier in product development to identify things that can be done to improve or reduce this concern.
Now, you’re integrating the information into your product development process. So, there’s a really nice loop that’s going on for the entire product development and manufacturing system to help each other with the processes.
Similar things can be applied to GD&T (geometric dimensioning and tolerancing). Maybe drilling holes in certain locations using certain surfaces or gauge points is more problematic. So that, again, can be fed back into the calculations. That might indicate that, look, this seems to be a less sensitive or a less efficient way to drill this hole. Can different data points for your GD&T or your PMI improve future manufacturing activities? It is a really nice way things can interact together.
And I’ve seen examples of these things, like the body in white spot welding, where they’re using AI in the live twin area. So, when the sheet metal for a body in white comes in before it is spot-welded, they can assess it for the quality aspects, the flatness or the curvature, or the locations of holes or whatnot. And they can evaluate that as part of the process to see how it can be improved.
Why are certain parts coming in, maybe with a slight curvature? Then, they can figure out what happened to that part during the manufacturing, pressing, and forming processes. With that data, you can start doing root-cause analysis much more efficiently. A manufacturer can then figure things out and then improve them. Whereas before, you’d have to start from square one, which is, hey, let’s investigate this.
So, these are just some of the great examples where smart manufacturing really improved things.
Additional Resources
Drive production excellence with intelligent manufacturing
The automotive industry is facing unprecedented challenges, with rapid change and intense pressure to meet the demands of climate change, regulations, and consumers. Download Now
Modernize automotive factories with Siemens Smart Manufacturing solutions
Discover how automakers can transform their business with Smart Manufacturing solutions using state-of-the-art hardware and software to modernize production lines. Watch Now
Virtual Manufacturing Development for the Automotive Industry
Companies in the automotive industry are pushing to develop the next generation of autonomous, electric, connected, and shared vehicles. View Now