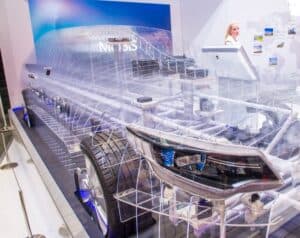
Manufacturers are looking into digital twins as a way to reduce the costs of commissions and improve client relations.
Manufacturers are investing in all types of advanced technology as a way to gain a competitive edge, reduce costs, and offer customers more tailored experiences. One of the key technologies being utilized by the manufacturing industry is virtual simulations, or digital twins, the usage of which has been trending upwards for a few years now and is starting to be embraced by manufacturers of all sizes.
Digital twins are virtual representations of objects; in this case machines. Manufacturers can use them to design, run, and test operations in a controlled, virtual setting before moving them onto the shop floor. The digital twin also gives manufacturers more insight into how operations will function in the medium and long-term, with sped-up tests to see how durable machines are, and how often parts need repaired.
SEE ALSO: You Can’t Spell Smart Manufacturing Without AI
Virtual commissioning, a term used by people in the manufacturing industry, is one of the fastest growing sub-sectors of the digital twins market. According to Phil Glennie, a director of marketing at Longterm Technology Services, there has been a noticeable uptick in the amount of manufacturers getting into advanced simulations and virtual commissioning in the past few years, he told Engineering.com.
Manufacturers can use virtual commissioning to preview a commission before testing on physical machines. This is similar to the process a lot of industries go through with clients, in which they show designs online and allow the client to make suggestions and changes, before a physical unit is made. Outside of reducing the cost, clients are also able to be present in more of the development process.
“People are looking to technology and simulation to be able to address those earlier on in the process,” said Graham Wloch, director of business development at Visual Components, told Engineering.com. “It creates a better, more optimized situation. You can go from putting out fires and being reactive to being proactive. A lot of our customers are trying to do that, to get ahead and mitigate those potential issues whenever possible,” he explained.
Even though the benefits of digital twins are applicable in manufacturing more than most industries, there is a conservative attitude towards adoption of leading-edge technology. A lot of manufacturers make large scale investments rarely, as equipment and technology upgrades can be costly. This is also coming at a time when manufacturers are struggling with a tough economic outlook, in which the cost of raw materials has increased quite rapidly.
Manufacturers are also struggling to acquire the talent necessary to make this digital transformation, with some having to use off-the-shelf services instead of developing their own. While this may be advisable in the short-term, in the long-term manufacturers need to have differentiators from the competition, and one of the key ways to do this is to have purpose built software.