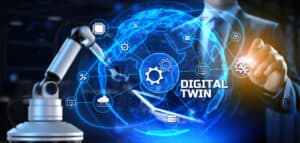
Virtual commissioning uses digital twins, sophisticated simulations, and modeling to help manufacturers adjust to changes and modernize their operations.
Auto manufacturers find they must often incorporate new technology into their work cells and production lines (e.g., make use of newer generation robotics systems as they become available), frequently change processes to fine-tune and improve production output, and quickly change lines to produce new models and variants of different vehicles. Increasingly, virtual commissioning is playing a larger role in accomplishing all of these things.
Virtual commissioning in manufacturing refers to the use of digital simulation models to replicate and test manufacturing processes, machines, work cells, production lines, or entire factories before implementing them in the real world. The technique allows manufacturers to validate and optimize the design and functioning of a manufacturing system without the need for physical prototypes or actual production facilities.
Such capabilities help automakers and part manufacturers explore multiple aspects of their operations all at once. Virtual commissioning use cases vary greatly from manufacturer to manufacturer. However, all applications deliver some common benefits in different operational aspects of a plant’s operations.
Probably the most common use of virtual commissioning is to simulate physical systems. Virtual commissioning lets a manufacturer create a detailed physical system replica that includes the workings of production machinery, robotics, and production processes. Such digital twins of these elements mimic their real-world counterparts.
Many aspects of production rely on the interplay between software that controls machines and processes and the hardware itself. Virtual commissioning gives manufacturers in the automotive industry the ability to evaluate software/hardware integration issues without deploying physical systems or installing any software.
The bottom line is that by using a virtual representation of production systems, auto manufacturers can significantly reduce the time and cost associated with physical prototyping and testing. And it lets them identify possible problems and inefficiencies, allowing them to fix these issues before actual implementation.
Going beyond the basics with virtual commissioning
Once a new work cell or production line is virtually created, virtual commissioning can take things to a higher level. For example, a barebones implementation would ensure that a production line, its hardware and software, and basic processes all work as specified. Using the same technology, a manufacturer could then test various aspects of the production process.
That might include using the digital twin to evaluate the performance and efficiency of different elements and processes. A manufacturer can try different what-if scenarios. They can explore things like what happens if they increase the speed of the production run. What if they swap one robotic system for another with more capabilities and functions?
More importantly, the simulations can test machine interactions and try out different things to optimize efficiency. Such testing can also be used to validate designs and processes before anything is deployed or installed.
Such capabilities give automakers and parts manufacturers a level offlexibility they have never had before. They can virtually try different configurations, workflows, and scenarios. That allows them to explore and evaluate different options and choose the most efficient one.
Virtual commissioning also helps with regard to another aspect of modern manufacturing. Namely, manufacturers must frequently make changes to existing production lines, increase the capacity of existing lines, or add new ones to accommodate changing market conditions. As we previously reported, a good example of this is Subaru’s decision at the end of last year to completely halt production of plug-in-hybrid vehicles as part of its clean-energy product offerings.
In such cases, virtual commissioning can help reduce risks when adding new manufacturing lines or modifying existing ones. Potential problems can be identified and addressed in the virtual environment, minimizing the risk of costly errors or downtime in the actual production environment.
Other factors to consider
Auto manufacturers, like many companies in other industries, face a work shortage problem. It is increasingly harder to hire people with the right skills needed in modern manufacturing environments. And, in general, companies find it harder to retain good talent.
Virtual commissioning can help in these areas, too. Virtual commissioning can also be used for training purposes, allowing operators and technicians to familiarize themselves with new systems and processes in a risk-free environment. That lets a manufacturer address any concerns workers have about using new technologies, and it can help upskill existing workforces, training them on new technology as it is implemented.
Getting the right technology in place
Virtual commissioning uses digital twins, sophisticated simulations, and modeling to help manufacturers adjust to changes and modernize their operations. The concept aligns well with the principles of smart manufacturing and Industry 4.0, which emphasizes digitalization, automation, and data-driven decision-making in manufacturing.
While any company can embark on its own virtual commissioning journey, most lack the time, resources, or skills to put something together. For that reason, many organizations undertake such efforts by teaming with a partner that offers technology solutions and deep auto manufacturing industry expertise.
These are areas where Siemens can help auto manufacturers modernize their manufacturing process. The Siemens smart manufacturing solution can help manufacturers monitor performance and predict operational issues in real time by using sensors, smart devices, and IIoT technologies. Additionally, Siemens lets manufacturers leverage virtual replications of their entire production plan to eliminate the iterative element of physical commissioning.
Additional Resources
Drive production excellence with intelligent manufacturing
The automotive industry is facing unprecedented challenges, with rapid change and intense pressure to meet the demands of climate change, regulations, and consumers. Download Now
Modernize automotive factories with Siemens Smart Manufacturing solutions
Discover how automakers can transform their business with Smart Manufacturing solutions using state-of-the-art hardware and software to modernize production lines. Watch Now
Virtual Manufacturing Development for the Automotive Industry
Companies in the automotive industry are pushing to develop the next generation of autonomous, electric, connected, and shared vehicles. View Now