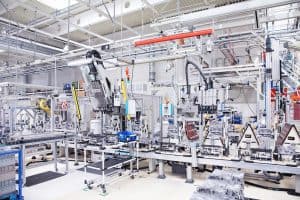
A look at how IoT and analytics can improve and enhance the performance monitoring of industrial equipment and processes.
Many industrial organizations are looking to digitalization efforts to help improve operations and increase efficiencies. One prime area getting great attention is using IoT and analytics to improve and enhance the performance monitoring of industrial equipment and processes.
RTInsights recently sat down with Andreas Steidele, Senior Enterprise Sales Executive at Siemens. We discussed the industry challenges to performance monitoring, how Siemens MindSphere can help, and the benefits of using such an IoT solution. Here is a summary of our conversation.
RTInsights: What are the industry challenges when it comes to performance monitoring?
Steidele: For years, one of the biggest challenges manufacturers have faced is the manual input of data using paper-based tools. I think the most used tool is still Excel. And this, of course, is a tool that is not appropriate for digitalization. You get human errors and transcription problems. You can never be sure that your data is true.
Another challenge arises from the lack of standardization of data capturing methods. If you have many different tools in your company, these tools may all work differently and have different algorithms to capture and present data.
The equipment landscape is also a challenge because, especially in bigger plants, they have inherited or brought in many different types of equipment. They have a heterogeneous equipment landscape that includes different hardware and software. That makes it hard to connect to each device and get the data out of your equipment at all.
Then finally, the last challenge is the missing intelligence that you need to make your data insightful and available, so you can draw your conclusions and get value from it.
RTInsights: What technologies and what solutions from Siemens help address these challenges?
Steidele: Siemens offers the industrial IoT as a service solution called MindSphere, which is hosted in the cloud. It maintains a repository of data that you send from your equipment and machines up to the cloud. The data is in a specific data model. It is defined according to your assets and machines and has context around it.
Then on top of this, we have MindSphere applications. These applications use the data in MindSphere to run analytics and other functions. In the case of performance management, it displays the KPIs that you defined and gives you data about how your machines are behaving in terms of quality, performance, and maintenance.
We have several applications that work together to create a very robust performance monitoring solution:
- SIMATIC Notifier delivers alerts and lets managers track and monitor the condition of their machines worldwide. It lets you set thresholds and monitor time-series data in MindSphere. A manager can implement a workflow within the app based on that data.
- SIMATIC Performance Insight provides machine and plant performance at a glance. Managers can access the complete performance overview of their machines, production lines, and global plants using the app. Managers also can monitor performance indicators over time and analyze data in, for example, select time periods to detect unused performance potential.
- SIMATIC Collaboration Board offers a collaborative solution to address production issues. The app lets managers share problems and solutions across teams and sites. They also can assign and manage tasks, as well as track the status of problems and solutions.
MindSphere integrates the capabilities of these applications and allows users to set up end-to-end workflows for performance monitoring. With the solution, a typical situation might be that a manager gets an alert something is amiss. The manager views and analyzes KPIs and other metrics to try to understand the problem. Next, the manager can search the collaborative database to see if a solution to the identified problem already exists. If not, they can use different methods to solve the problem, documenting what worked so anyone encountering the issue in the future can benefit from their work.
RTInsights: What are the benefits when such an IoT solution is used?
Steidele: If you have the right IoT solution, all your assets are connected, and you are sending data to a cloud space. In that way, it’s not available only locally, but globally so you can access this data from wherever you are in the world. This is probably the biggest advantage of MindSphere. You have data available globally to connect your machines or assets via the IoT protocols in a very simple way.
Then, you can use this data and go a step further. You can drill down into the analytics and use them to identify and solve problems with your machines. If your machines are not performing well, your throughput is down. Performance monitoring through MindSphere provides a powerful tool to ensure your quality meets expectations and that you can take action and make continuous improvements to performance, quality, etc.
One other thing to note is that performance monitoring and the collaborative capabilities of MindSphere offer immediate improvements, and they can be the cornerstone for companies that are undertaking a digital transformation.
RTInsights: Can you give some examples of how these benefits are realized?
Steidele: I’ll give you a simple example, maintenance. If you imagine before IoT, whenever there was a problem with the machine, the company had to call the service line. Then, some technician had to answer the phone and figure out what’s wrong with the machine. Most likely, they had to send people onsite, see what’s going on, and then try to repair it.
With new digitalization efforts using IoT, you can have this data available at the service location. There is no need to send somebody out to see what’s going on. You have this virtual insight into the machine, into the machine’s parameters, into the machine’s behavior, from another location. You can draw your conclusions, and then, if you need to fix it via an update, service update, software, bug fix, hot fix, whatever it is, you can do this remotely. Or, if it cannot be done remotely, the service technician arrives already knowing what to look for.
So, service and maintenance work can often be done virtually and quicker. This delivers great cost savings because you save time, traveling, and man-hours.
Another example is performance. When everything was onsite, you could only look at the performance data of a single machine or a single plant. It was hard to compare the performance of lines or plants from somewhere else because the data usually was not available globally. Worse, the data was collected in different manners from site to site, so everybody had their own calculation efforts.
With performance monitoring with the industrial IoT, you can measure every site or every line the same way. That lets you compare your data because you have one source of truth. So, you can benchmark the performance of your lines and plants. You can draw conclusions and see which recipe runs best, which shift runs best, or who might need some education to learn how to operate their machine line more efficiently.