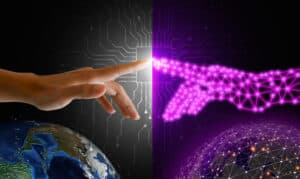
By running simulations of different scenarios, a digital twin offers an accurate reflection of the current state versus the future state and can provide the insights needed for making evidence-based decisions.
Digital twins have become a major part of operational excellence in recent years. Originally developed as a way to replicate the physical world in virtual form, they now play a prominent role in forecasting and planning future scenarios. Their adoption is also extremely varied, from manufacturing plants identifying bottlenecks in production, contact centers allocating resources to manage surges in demand, hospitals looking to reduce a backlog of appointments, or indeed any type of business looking to combat operational inefficiencies – there’s a twin for them all.
So much so that it’s become something of a buzzword, but there are other relevant buzzwords here too. For one, every new piece of technology now seems to have artificial intelligence and machine learning as part of its engine, developing highly targeted insights on which to build more personalized or sophisticated services. And for anyone keen on identifying the most helpful business intelligence available to improve decision-making within an organization, process mining has also become a must-have. This technology will ensure that you are automating and then leveraging the capture of all the pertinent data moving through your day-to-day operations.
No doubt, each technology can offer great benefits to a business independently, but what happens if we combine all three? After all, they are very compatible. In other words, we would be creating a digital twin that is constructed with the intelligence of process mining and built using the power of machine learning. This moves things on significantly, not only increasing automation but it also offers the possibility to take digital twins beyond prediction-based planning and into prescriptive analytics; a tool with which to run simulations that will tell you exactly what the best corrective action is to take.
This may seem like something for tomorrow, but let’s take a look at the three technologies now and see how they can, in fact, already be combined to create what you might call a next-generation simulation engine.
See also: Digital Twins, IT/OT Convergence Drive the Industrial Internet
Understanding Digital Twins
The basic premise of digital twins is simple. A physical object or process that is fitted with sensors will provide information to map out a virtual replica, or twin. For example, a picking system in a warehouse facility. Or alternatively, the focus of the twin could be on resources, such as the availability of staff or equipment. Or it could be activity-led information, such as employees’ movement through a workplace or the time needed to complete a task. This type of information can be qualitative as well as quantitative and will provide sufficient input to create an effective digital twin, which you can then build on as you test things further.
The twin will run alongside the real-life version. Since it is a replica but in digital format, it can be used to simulate alternative scenarios to test ways to streamline a process or troubleshoot possible challenges without disrupting real-world operations. In doing so, it provides the perfect accomplice to extremely accurate testing and decision making. By running simulations of different scenarios, the digital twin offers an accurate reflection of the current state versus the future state and can provide the insights needed for making evidence-based decisions.
Process Mining
Process mining gets to the heart of what’s happening within any IT system. It does this by monitoring and analyzing real-life processes constantly and ‘mining’ the information to gather insights. A lot of businesses will use it as a tool of discovery, highlighting areas of inefficiency that they can work to improve. It can also be used as a tool for conformance, which means benchmarking current processes against desired standards, usually for the purpose of meeting compliance obligations.
While important, these two types of applications don’t really make full use of process mining’s potential, however. With its capabilities of identifying and leveraging business information, bringing it all together into one place, process mining makes a perfect partner for constructing digital twins with the most pertinent and up-to-date data. From there, it can be used in combination with simulation. Projects will no longer be fixed with a beginning and an end, but instead, process mining can be used to achieve continuous improvement. Organizations will use mined data as the basis for future-looking simulation models that will be designed to always keep businesses as lean and productive as possible.
Machine-learning
Where does machine learning fit in? Through machine learning, it becomes possible to create digital twins automatically without the need for physical intervention. A machine learning tool will work out the decision rules of a system and understand how that system is built. From there, it can follow these insights to automatically create and optimize its own digital twins.
If you feed the machine learning with information and insights gathered from process mining, you’ve created a digital twin far quicker than you would have been able to with a manual approach. Furthermore, this advanced digital twin can be fed with the most up-to-date information, so it will know as soon as the process has changed in any way and take appropriate action, whether that’s corrective or it’s just time to update.
See also: Digital Twins Require Their Own Special Brand of Security
The next-generation simulation engine
By reaching these new levels of speed, power, and accuracy, process excellence becomes attainable for all organizations. This is where we can see the possibility for continuous assessment and auto-tuning of performance. A digital twin that operates in this way will be able to predict a crisis before it happens, self-assess, and then adapt to help defuse a potentially critical situation. It’s a new level of technological maturity, and thanks to the compatibility of these impressive tools, it is already available.