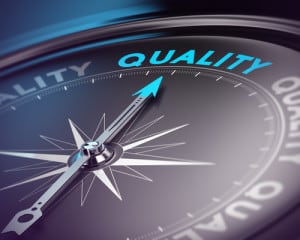
How an IoT intelligence platform provided a path to ensure quality assurance tolerance limits always remained at the highest level.
Organization: Global adhesive manufacturer
Industry: Aviation, automotive and electronics.
Business Opportunity or Challenge Encountered
One of the world’s largest adhesive manufacturers, with over 130 plants across Europe, the Americas and Asia offers sophisticated adhesives for sensitive applications in aviation, automotive and electronics, was in a quality assurance quandary.
Quality control is very strict at this manufacturer. There are places and uses for adhesives that are both sensitive and critical in nature, such as the aircraft manufacturing sector where safety and integrity is paramount. Although this manufacturer was always functioning above industry minimum required tolerances, it also was regularly reducing its internal Quality Assurance (QA) tolerance limits, contrary to the manufacturer’s internal standard.
A wide array of parameters influences adhesive quality such as raw material quality input, the variations allowed in the raw material weight, ambient conditions, and numerous process control parameters like temperature, pressure, and mixer RPM.
How This Business Opportunity or Challenge Was Met:
This manufacturer needed a holistic perspective on these functions in order to ensure that its QA tolerance limits always remained at the highest level. Flutura was brought in to assess the situation and revealed that in places there was a lack of understanding of the sensitivity of these QA parameters and how they affected output quality.
It also discovered that there was room for improvement in monitoring and controlling the process in real-time. These situations were leading to variations in reduced yields resulting in a build up of inventories, missed customer deadlines, and loss of significant revenue. On its path to a solution, Flutura broke this problem down into the following three questions:
- Which process parameters influence quality outcomes and which process parameters do not influence quality outcomes? ( Distill signal from noise )
- Of the process parameters that influence quality outcomes, what is the degree of influence for each? ( Rank order parameter influence )
- What is the next best action to take once a process degradation is expected?
Flutura’s Cerebra IoT signal intelligence platform analyzed over three years of process and sensor data at the manufacturer, garnered from various sensors (temperature, flow rates, viscosity and pressure) that were monitoring industrial mixers. Cerebra’s episode detection algorithms, or its deep learning, filtered signal from noise and quickly identified the contributors to a reduction in quality; what Flutura calls anomaly signatures. These signatures are used as signals to predict future degradation of quality.
Cerebra’s proprietary N-dimensional Euclidian distance-based scoring algorithms normalized and presented a unified score that was presented to the business team. This unified health score provided the process team with a different view of internal goings on to benchmark, specifically target and radically improve process efficiencies.
Cerebra’s ensemble models predicted potential quality failures allowing the operations team to take real-time actions to control process deviations. This process was scaled to 33 plants, 1,400 manufacturing lines and 16 event types cumulatively streamed in 20 million sensor events analyzed.
Measurable/Quantifiable and “Soft” Benefits from This Initiative:
The enhanced quality report completed by Cerebra provided the manufacturer with a more proactive, quality assurance model, helping the company move away from the more reactive quality inspection model. This philosophical shift provided actionable insights to identify and eliminate quality bottlenecks before they would occur.
Ultimately, the roll out of Cerebra’s findings to 350 lines across 33 manufacturing plants, and 15 countries is a major positive outcome for this business. The scale of the solution has addressed a problem that has the potential to ultimately save the company over $300 million globally.