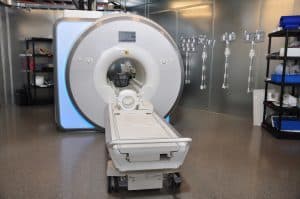
IoT offers a way to remotely monitor and manage medical devices, and can enable new business models for device manufacturers.
There is growing interest in using the Internet of Things (IoT) in medical devices. The data gathered with IoT-enabled medical devices—the so-called Internet of Medical Things (IoMT) devices—can be used to remotely monitor and fix devices. The use of IoT brings numerous benefits. Medical device manufacturers can incorporate data collected from their fleet of products in the field into product design considerations. They can also leverage the data to offer innovative services that differentiate them from the competition.
To get a better understanding of how advanced technologies like IoT are being used to connect medical devices remotely, we recently sat down with Rene Zoelfl, Business Development Director, PTC.
We explored the role of IoT in medical devices for remote management, how the technology is being used, how the technology can support new business models, and then covered some real-world examples of the IoMT in action.
What are the key technologies?
RTInsights: How can manufacturers, healthcare facilities, and patients best benefit from remote monitoring?
Zoelfl: I would say remote monitoring gives two main benefits. One is remote monitoring lets device manufacturers optimize their processes, and the other benefit is that they can optimize the relationship with their customers, clients, and patients. These things can help transform the way they are doing business.
What are the key advanced technologies that are enabling innovations in the design and use of remote devices? On one hand, we have IoT technologies that enable connectivity, advanced analytics or artificial intelligence, and the ability to automate decisions and processes to a higher level. The other key element, the other key technology, I’d like to highlight is augmented reality, which gives us a different way, a different capability, to interact with equipment in the context of its use and in the context of the location where it is used.
How are these technologies used?
RTInsights: How can companies use these technologies in the product life cycle?
Zoelfl: There are multiple ways. Where to begin?
A manufacturer can use IoT technologies internally. They can make sure that when teams are working together on the design of new products, they can more easily communicate and get access to the generated data. Then they also could have the same capabilities or the same technologies to use when it comes to handing over that information into manufacturing.
For instance, when a manufacturer thinks about non-conformances that might occur in the manufacturing process, because of maybe some difficult designs, or maybe some materials that they have selected, they can feed that information back into the development and engineering organizations. They can react much faster before the product might have left the company and not when it is at the patient or the caregiving facility.
They also could use it in sales processes. For example, they could use augmented reality to demonstrate a certain asset’s capabilities in the context of where it should be used and without actually having a physical product there. So, they use the product data like CAD data that has been generated. For instance, they can use it and see what kind of planning is needed for that asset to fit in the facility that has been designated to house that equipment. They could also demonstrate what the performance would be, how the device is used, how it can be operated without having a physical asset.
And then, of course, when it comes to optimizing the service processes, I would say this is the biggest benefit for the manufacturer. The device manufacturer can base service on the technology using the connection to the device once it is in the field. They can use that information to optimize their service processes. For example, medical device manufacturers could use IoT technology to observe the devices in the field and do reporting. These processes can automate based on the data that the device is giving us.
The manufacturer also could ensure, for instance, that the service technician dispatched to maintain, update, or fix a device has the right spare part or at least the right information of what should be fixed. Even better, a manufacturer can use the technology to resolve some of the issues remotely without even sending a high-paid service technician to the asset in a hospital. Then they also can use data to optimize the product itself. For instance, a manufacturer could see if the assumptions made when designing the product are still valid. Or is the device, is the asset used as they thought it would be used?
Other issues also can be addressed using remotely collected data about the device. Is it reliable enough from a design perspective? A manufacturer might find that the overall lifetime of the product is much lower than the reliability designed into that product. They can use the data to shift the business models and argue, “Instead of selling the asset to your hospital or your patient, you can pay per use, per treatment, or per image.”
Hospitals and laboratories also benefit from these technologies because the technicians in the hospitals can be enabled to do some tasks by themselves. For example, the manufacturer could enhance self-service capabilities, which increases customer satisfaction with the device. And in the end, the hospital or lab benefits from a higher uptime of the asset. They do not need to adjust their plans or schedules. They can use the device when needed instead of running the risk of the device not being available.
What enhanced services are possible?
RTInsights: What are some of the add-on services companies might offer using the technologies you’ve talked about?
Zoelfl: We have one customer that sells in vitro diagnostic analyzers and equipment. They have shifted to a more data-based business model.
To start, they are charging the lab by the number of tests the lab run. They also are taking insights they have gathered from the devices they have sold in the past to the customers. With this information, they can help to optimize the workflow in the lab for the benefit of the customer. Such advice is possible because they could identify inefficiencies that maybe the lab manager or the lab operator doesn’t recognize. That’s a huge benefit because the lab operator, or even a hospital, has limited data available and data that their facility is generating. The benefit for the manufacturer of the assets is that they have the whole fleet of devices that are in the field available as data sets. And with that, they have a much broader view, much better capabilities to derive the right conclusions out of the data.
Another customer of ours is using augmented reality whenever it ships a diagnostic device. An augmented reality experience on a tablet guides technicians, either clinical or lab or company technician through some of the tasks. What is the benefit? The benefit is that the lab or the hospital doesn’t have to call a service technician from the manufacturer, but instead, they can do some of the routine tasks by themselves. Additionally, the manufacturer saves money since its technicians do not have to travel to perform routine tasks or the tasks performed at the customer are more efficient.
What are some use cases?
RTInsights: Can you give us some use case examples of these technologies in action?
Zoelfl: We have multiple customers that are really relying on the capabilities of the technology we are providing.
One is Elekta. Elekta is a manufacturer of expensive radiation equipment. They are using the information they can gather from their assets to guarantee uptime for the hospital. Using our solutions, they have greatly increased the number of remotely resolved service issues. They also reduced the mean time to resolution of issues by up to 30 percent. Part of that success is attributed to the fact that 50 percent of issues could be resolved remotely. They also run approximately 600 preventive actions per year because of the data that they are gathering. And with that, they positively impact more than 14,000 patients because the devices were up and running when the patient needed the treatment. So, the patient doesn’t need to be sent home to come back later because a device was not working.
An additional benefit of having machine data for its lifetime is that service employees are better prepared. Without data, they had limited insight into the equipment performance and the status and the conditions of the equipment. The usual scenario was the device was down, or the equipment was down. The hospital called Elekta, and Elekta sent a service technician to fix the device. Key indicators, like the mean time to repair or first-time fix rate, were very low. Using a device’s data, the company can take a more proactive service approach.
Another example is Illumina. Illumina provides genome sequencing technologies and services for life science research, translational and consumer genomics, and molecular diagnostics. Its solutions are used in a broad range of areas, from cancer research to agriculture. Its challenge was that the downtime of the scientific and research equipment it sold reduced a lab or hospital’s productivity and throughput. And in some cases, the consequences can be more severe. They implemented a solution based on our technology and where they were now able to get a 360-degree view on the asset through IoT monitoring. They also made the operational data available to the persons that need it inside and outside of Illumina. And they also integrated that with other existing systems, like, for instance, their salesforce.com implementation.
They also could have the operational data now available on demand. So, whenever they walk into a facility, they had the operational information. They also have real-time insights and historical trends, which they can also deliver direct to the customer. Using the information could help optimize workflows and decrease their labor hours by 10 percent. They also decreased preventable failures by 5 percent. And the first-time fixed rate was increased by 9 percent.
Another example is Varian, which is a manufacturer of radiotherapy or radiosurgery, proton therapy devices. It is one of the leaders in oncology treatment. Varian had the challenge that system and equipment problems typically required one or more service technicians to diagnose and resolve issues in the hospital. Problem resolution can be complicated in case incorrect or incomplete information has been provided. In typical treatment environments, the loss of one day of treatment time means up to 35 patients miss their treatments.
They implemented ThingWorx to launch their SmartConnect solution. The solution helps Varian to manage approximately 28,000 devices and 90,000 alarms per month. They also integrated the data with Salesforce. So, the data that the device or the equipment generates doesn’t need to be entered manually into Salesforce because now, the data can be transferred to Salesforce automatically. They also see the information, gathered from the devices based on the ThingWorx measurements, embedded into the Salesforce user interface.
Varian has had huge success with its SmartConnect solutions. The number of customers using SmartConnect has quadrupled in the last year. They now have SmartConnect-enabled systems deployed in more than one and a half thousand treatment centers. There’s an average use of this equipment of 4,000 hours per month. They have shortened their response time to repair and remotely diagnose problems, in many cases resolving the issues without the need for a site visit. The average response time of four hours has been reduced to two hours based on the SmartConnect-enabled systems. That reduction can save a hospital more than $2,000 per unit.
Final thoughts
RTInsights: Any final thoughts?
Zoelfl: I think some might argue that there isn’t a big difference between IoT and IoMT. I would argue that there are some differences because of the data, the handling of the data, and criticality of the product. So, some different capabilities need to be considered. For instance, you must ensure that equipment is in a safe state before you perform a remote software update or remotely try to solve an issue with the device.
With medical equipment, there is great interest in using IoT to support expensive equipment. But smaller medical devices can sometimes benefit from the IoT in even more ways than expected. In general, I would say this is an inspiring time for the IoMT to really show its worth in the industry, and we at PTC are excited to take our great experience we have with remote monitoring devices and equipment to support even more customers across a wider reach.
Learn more about remote monitoring for healthcare organizations on July 30th when Salvatore Salamone, Editor-in-Chief, RTInsights hosts an interactive discussion with Dr. Joerg Traub, CEO of Forum MedTech Pharma, and Rene Zoelfl, Chairman of the PTC Healthcare Executive Advisory Council. Register for the webinar now.