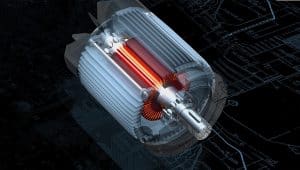
Use of digital twin technology in manufacturing is moving beyond design to also include downstream applications that help improve the production process.
Interest in digital twin technology is on the rise. New use cases are emerging. And like any nascent market, there is a need for a trusted source of information and leadership to validate best practices and guide the development of standards. Enter the Digital Twin Consortium, an Object Management Group (OMG) organization that brings together industry, government, and academia to drive consistency in vocabulary, architecture, security, and interoperability of digital twin technology.
RTInsights has teamed with the Digital Twin Consortium to develop a series of interviews with some of the people leading the effort. We recently spoke with Sameer Kher, senior director of product development at Ansys, one of the consortium founding members. Kher serves on the consortium’s steering committee. Here is a summary of our discussion with Kher.
RTInsights: How did Ansys first get involved in digital twins?
Kher: As you probably know, Ansys is the leading provider of simulation software in the world. For many years, simulation software has been used by companies to design and make products, create better products, create products that have more functionality, and get to market faster. The simulation software essentially replaces physical testing. That’s been the traditional use of Ansys.
Over the last few years, what we’ve seen, though, is the use of simulation in additional use cases further downstream, after the product design is completed. Simulation is now being used in manufacturing and operations in making sure that you manufacture the product in the best way possible and then make sure that you operate the product in a very efficient way. That’s where the Digital Twin journey started for us, essentially through a few early adopters who saw the potential for how simulation plays a role in other areas, not just the product design process.
RTInsights: What is unique about Ansys’ digital twin solution?
Kher: At Ansys, we’ve come up with a solution that lets you very quickly build, validate, and deploy simulation-based digital twins. We believe the main value that digital twins unlock are through analytics and insights that you get into your product.
There are many different ways and a lot of different pieces of information that go into building a digital twin—everything from maintenance records to asset identifiers. One component of that is the analytics piece that unlocks all the value. And there you have either data that you can use and build correlations. Or you can use what we promote, this physics-based approach, where you can use simulation and techniques combined with data to really get to the depth of insight that you need.
That information lets you do better predictive maintenance and better manage costs, like warranty costs and things like that. The analytics and insights also help you better operate equipment to get more profitability and revenue out of your equipment.
To do that, you could use just data, which many companies do, but data is limited because you often don’t see the failure modes, and you don’t drive equipment to failure. Also, the time that equipment needs to be in the field to generate meaningful data is high. Another limitation of only using data is that you may only have a few pieces of equipment, and you can’t really wait for the data.
Simulation is a way to get much deeper insights. You get data and information even without operating that equipment. So, using a digital twin, you can get a lot more data, a lot quicker. And you get a higher level of accuracy.
That’s unique about what we do. With Twin Builder, what we’ve also done is made it easy to reuse all of your engineering know-how to build your digital twin. We let you validate it using sensor streams. And we let you deploy it into modern architectures using containers and other methods so that your digital twins can scale with your assets.
RTInsights: What industries most benefit from digital twins today?
Kher: We see digital twins being used across many different industries today. We see today’s interest and uptake are highest perhaps in manufacturing, both in discreet and process manufacturing. Second, probably is oil and gas and chemical processing types of industries. And then probably the third most common area is in automotive, where complicated drive trains and autonomous vehicles require digital twins, particularly simulation-based digital twins, to operate efficiently.
RTInsights: What industries do you think will benefit from digital twins in the future?
Kher: I think every single industry is about to be disrupted quite heavily with digital twins. While we see faster adoption, at least in our space, in the three industries I just mentioned, we have activities across all industries. It covers everything from aerospace and defense to manufacturing. It is all industries that you can think of all the way up to even consumer packaged goods. Everything has an opportunity to be disrupted by digital twins. For example, healthcare is another one where we see a lot of interest in digital twins and a lot of adoption going on right now. So, I expect digital twins to be adopted increasingly by nearly every industry you can think of.
RTInsights: What do you think the digital twin industry will look like in 5 years?
Kher: Five years from now, I would expect digital twins to have permeated quite a bit in most of our target industries. I see activities like remote monitoring of manufacturing equipment, virtual commissioning, and change-over of production lines in manufacturing to be very commonly done using digital twins. Activities like training new operators and the institutionalization of know-how of when equipment is about to fail, and those kinds of things, to become possible through, or much easier to access, through digital twins. I also think equipment and processes that are being developed or even sold across customers, from one customer to another, will include a digital twin. In that way, you get the physical asset, a physical piece of equipment, but perhaps more valuable. You’ll start seeing customers also provide the digital equivalent, which perhaps is even more valuable. I think digital twins will be everywhere.