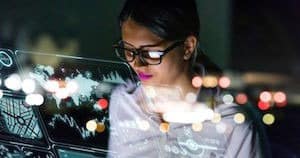
Intelligent remote monitoring of products provides real-time data that enables companies to identify potential issues, troubleshoot errors, and resolve anomalous conditions. This is made possible through a new generation of intelligent IoT platforms that provide secure, embeddable, and easily deployable connections to sensors, devices and equipment across network topologies and communication scenarios.
A New Era for Remote Monitoring
Remote monitoring has been around for some time, dating back to when much of remote monitoring technology was analog-based. The aim has been to provide in-depth views of analytics and enable users to react to real-time events, preferably with some level of automation. Remote monitoring is used in a variety of systems at hospitals, industrial plants, data centers, and in vehicles. Configurations may include devices and systems inside and outside the enterprise, such as sensors, embedded systems, applications, mobile phones and wearables. With in-depth views and insights into events in real time, enterprises are able to update and upgrade products after they are already out in the field, often without any inconvenience or disruption to customers.
[Download the PDF version of this report]
The rise of the cloud, IoT, advanced analytics, artificial intelligence and machine learning has added a whole new dimension to remote monitoring. Enterprises are increasingly moving to the cloud to support their IoT ambitions. Leveraging IoT-based data streams not only means increased visibility into events taking place across an ecosystem, but also opens doors to new business models based on continuous improvement and responsive service.
There has been a revolution in remote monitoring (tied to the digital age and the rise of IoT and advanced analytics) in which digital data now flows from every corner of the enterprise. “Monitoring services available 10 years ago were desktop-based, limited in data output, and largely reactionary – depended on humans to interpret what was wrong,” writes Victor Avelar, Senior Research Analyst at Schneider Electric’s Data Center Science Center. “Digital remote monitoring has resolved these limitations through technology, and over the next few years more limitations will be addressed by technology.”
In addition, today’s remote monitoring provides opportunities to share device- or sensor-generated data with customers and partners through a platform approach, opening up new lines of business and opportunities for innovation. Companies can not only produce products, but can also offer ongoing service contracts that include monitoring and maintenance. Data collected through intelligent remote monitoring is integral to the connected enterprise, providing opportunities for customer service, revenue generation, customer loyalty, and ultimately, competitive differentiation.
Intelligent Remote Monitoring Delivers Value to the Business
Intelligent remote monitoring – in combination with IoT and advanced analytics – is more than just collecting data on product performance. It’s about transformation – transformation of technology architecture and transformation of processes. It’s about building new revenue streams or taking the business in new directions that were not possible before. It’s about taking data from these systems and providing analysis that adds predictive and prescriptive power, which are highly sought-after value-added services. “In many companies, smart, connected products will force the fundamental question, ‘What business am I in?’,” write Michael E. Porter, economist at Harvard Business School, and James E. Heppelmann, President and Chief Executive Officer at PTC, in Harvard Business Review.
In recent years, many manufacturers have successfully captured data streams from various parts of their operations – from production systems to data centers to warehouse sensors. As a result, they can continuously improve and enhance their products while they are still in the design stage. Such data can also play a predictive role, using pattern matching algorithms to determine when faults may occur, before they occur. Customers can pay for value-added services for these intelligent maintenance approaches.
Today’s intelligent remote monitoring solutions provide capabilities that:
- Track asset readings and usage data
- Capture critical alert notifications
- Monitor assets for leading indicators of issues
- Learn normal behavior and detect anomalies
- Leverage data from connected products
- View and analyze sensor data and alert histories
- Troubleshoot alerts by viewing multiple reports on sensor data
Intelligent remote monitoring is the ideal response to a highly competitive business landscape in which customers expect the highest possible levels of service at reasonable costs. They prefer to purchase outcomes from manufacturers, not products. Offering smart, connected products helps build a positive relationship with today’s customers, while providing essential information to continuously improve and innovate. This results in a range of business benefits, described below.
- Improve Customer Satisfaction
Intelligent remote monitoring enables companies to leverage data from connected products for improved service, support and usability, which leads to increased customer satisfaction. The technology helps companies to remediate service issues and make service strategy decisions using contextual information, such as installed base performance and service resolution times. Connecting and monitoring products or assets enables opportunities such as optimizing service delivery and predictive analytics. These initiatives create a higher level of trust and satisfaction with customers by changing from a reactive to a proactive service model. Essentially, the equipment self-reports issues, rather than the customer – and this is a powerful case for a superior customer experience.
- Achieve Competitive Differentiation
Intelligent remote monitoring boosts the pace of product and service innovation. Real-time data monitoring also enhances engagements with customers, paving the way for greater interaction and higher-quality service. Importantly, a new generation of remote monitoring tools and platforms delivers insights that can be acted on automatically, providing immediate responsiveness. Service operations are quickly becoming the new profit centers for today’s global manufacturers. “The importance of manufacturers transforming themselves from sellers of products to deliverers of services is becoming more clear as companies strive for new ways to please customers – and hang onto them,” report the authors of the Annual Manufacturing Report 2017. The survey report finds 44 percent of manufacturing executives say they are moving in this direction, and 17 percent already consider their efforts to be “advanced.”
- Increase Innovation and Drive New Revenue Streams
Intelligent remote monitoring offers ways to not only improve operations, but open up new lines of business as well. It also enables people to become more engaged with the business. The connectedness that intelligent remote monitoring delivers provides information to the people who need it, when they need it. As a result, not only can they make more accurate and well-informed decisions, but they may also begin asking questions that they were never been able to ask previously. For example, what happens if a workflow is changed with fewer signoffs? What if products are shipped differently? What if a product is enhanced with a certain feature for certain markets?
- Reduce Costs
Intelligent remote monitoring helps lower service delivery costs, reduce travel costs with fewer onsite service calls and truck rolls, as well as increase technician efficiency. Companies can monitor the status of equipment, devices and systems in the field for maintenance or updating. Organizations with intelligent remote monitoring will see reduced overhead in operations and maintenance, as fewer live visits from technicians will be required. When technician visits are required, information and diagnostics can be provided beforehand to shorten the length of the visit and reduce downtime.
- Operate More Efficiently
Typically, organizations have not had visibility into what happens to machines or products once they are put to use until problems are reported. And, when things break down in machines, factories or vehicles, it can lead to great expenses.
Intelligent remote monitoring helps companies gain insight into equipment performance to ensure asset availability by managing asset condition and use to preempt failures. Organizations can avoid equipment downtime by monitoring asset performance and condition, proactively avoid service issues whenever possible, as well as reduce service costs by avoiding costly onsite service visits. Technicians then need to be sent to internal production or customer sites to make needed repairs.
With sensors streaming performance data from machines or products into analytics systems, organizations may be able to predict when something is going to fail or is underperforming. In turn, this data can be fed back into the design and production stage of machines or products as part of a continuous improvement process. In addition, the recommendations and actions of technicians can be captured and digitized.
- Provide a Path to Predictive Analytics
Intelligent remote monitoring systems are paving a path to the deployment of support AI algorithms that can find patterns and recommend actions. When remote monitoring and cognitive systems work together, the results are powerful. Businesses benefit from systems that can process and analyze enormous amounts and varieties of data to find patterns, often in real time. For example, production data streams may show certain variances prior to a component failure. Or, time-series data may demonstrate that a machine gets higher levels of usage during certain times or days of the year, and resources can be adjusted accordingly.
Intelligent remote monitoring takes data gathering to the next level and enables systems to react in an autonomous fashion to events. In industrial environments, the combination of data from remote monitoring and machine learning will enable real-time responsiveness to anomalies that may arise with machinery or equipment. While transmitting data to a central data center or cloud may incur some degree of latency, machine learning algorithms within edge devices or systems where solutions reside can be optimized.
Intelligent Remote Monitoring in Action
There is no one size fits all for intelligent remote monitoring; its applications are as different as the organizations in which it is being implemented. Every industry – or even companies within the same industry – has different requirements that intelligent remote monitoring helps address.
- Up, Up and Away with New Services
A leading elevator manufacturer employed intelligent remote monitoring to keep its customer base on the move, and proactively fix problems before they affected the performance or availability of elevators. McKinley Equipment Corporation employs intelligent remote monitoring to enable alerts that trigger workflows, or to advise technicians of equipment issues via phone call, SMS message, or email. The company now employs sensors, IoT and advanced analytics to detect inoperable or failing parts and schedule maintenance calls before customers are even aware of problems. The key is to be able to monitor the performance of all elevators, and alert local technicians when problems appear imminent.
McKinley is already seeing benefits from having increased visibility into its installed base of equipment. While the service industry’s average first-time fix rate is around 60 percent, McKinley has achieved a rate of close to 90 percent. In the process, the company has evolved from manufacturer into a proactive service partner, providing continuous service. Additional IoT-enabled and advanced analytics-capable levels of visibility into customer operations also enable McKinley to predict part failures and optimize parts stock in its warehouses and technician vehicles – enhancing their first-time fix rate and maximizing equipment uptime. Data provided by the solution also will support diagnostics ahead of site visits.
- Medical Monitoring
Varian Medical Systems, Inc., a leading manufacturer of integrated cancer therapy systems, imaging systems and other medical equipment, knows the performance of its products is a matter of life or death. Such systems typically required one or more service technicians to diagnose and resolve issues at the treatment site, resulting in higher costs and lost patient treatment time. Operator input errors also may disable these systems. The loss of one day’s treatment time can result in 35 patients missing their treatments.
Over the past five years, with intelligent remote monitoring, Varian has been able to improve device performance through connectivity and predictive monitoring, reduce the number of technician visits per asset per year from 72 to 42, decrease on-site visits by 42 percent, and save $2,000 for each onsite visit avoided. Through intelligent remote monitoring, Varian directly and securely connects to customers’ systems when support is required, providing quick and accurate problem resolution.
The Varian SmartConnect-enabled systems are now deployed in more than 1,500 treatment centers across the globe, where they are used an average of 4,000 hours per month. With SmartConnect, Varian completely installs and maintains updates for its software product lines without requiring any field service support. The product’s remote service capabilities have helped grow software service contracts, which are currently captured at a rate that is 17 percent higher than hardware service contracts.
- At Your Service: Retail Robots
Bell and Howell, a communication systems and maintenance services provider, has taken proactive customer service to a whole new level with intelligent remote monitoring and IoT. This capability helps power and connect its Cleveron PackRobot intelligent locker system, currently deployed in the retail industry as Walmart’s Pickup Tower, a 16-foot autonomous self-service retrieval system that enables customers to pick up their online orders in a matter of seconds by scanning a code on their smartphone.
Bell and Howell maintains a continuous connection with PackRobot installations via the IoT, reducing equipment downtime, improving first-time fix rates and increasing overall performance. In addition, the company can capture metrics, such as the number of packages deposited into the machines, to facilitate predictive maintenance. Data is also shared with Bell and Howell customers.
Bell and Howell plans to expand such IoT-enabled capabilities across its entire product portfolio, hastening its evolution from a purely manufacturing company into a diverse services provider. Intelligent remote monitoring and the IoT are enabling the company to provide superior and proactive service to its customers, who often may not even be aware that a problem may have occurred with a machine.
Conclusion
Intelligent remote monitoring is an important step towards enhancing innovation and gaining more in-depth, real-time data that will drive insights. It is also the foundation of real-time analytics, and, increasingly artificial intelligence and machine learning. Intelligent remote monitoring enables decision systems to respond – instantaneously – to events with predictive and prescriptive insights.
At the same time, the rise of connected enterprises and ecosystems via the IoT, in conjunction with advanced analytics, is changing the face of the competitive landscape, leading to greater innovation through connected products as well as through connected operational systems. As a result, enterprises will see increases in reliability and efficiency. Smart, connected products, powered through intelligent remote monitoring, are changing the very nature of manufacturing, from pushing out products to that of 24-hour, seven-day-a-week service providers.
“The manufacturer, through access to product data and the ability to anticipate, reduce and repair failures, has an unprecedented ability to affect product performance and optimize service,” Porter and Heppelmann observe. “This opens up a spectrum of new business models for capturing value, from a version of the traditional ownership models where the customer benefits from the new service efficiencies to the product-as-a-service model in which the manufacturer maintains ownership and takes on full responsibility for the costs of product operation and service in return for an ongoing charge. These shifts will affect virtually every industry, directly or indirectly.”
Download the PDF version of this report